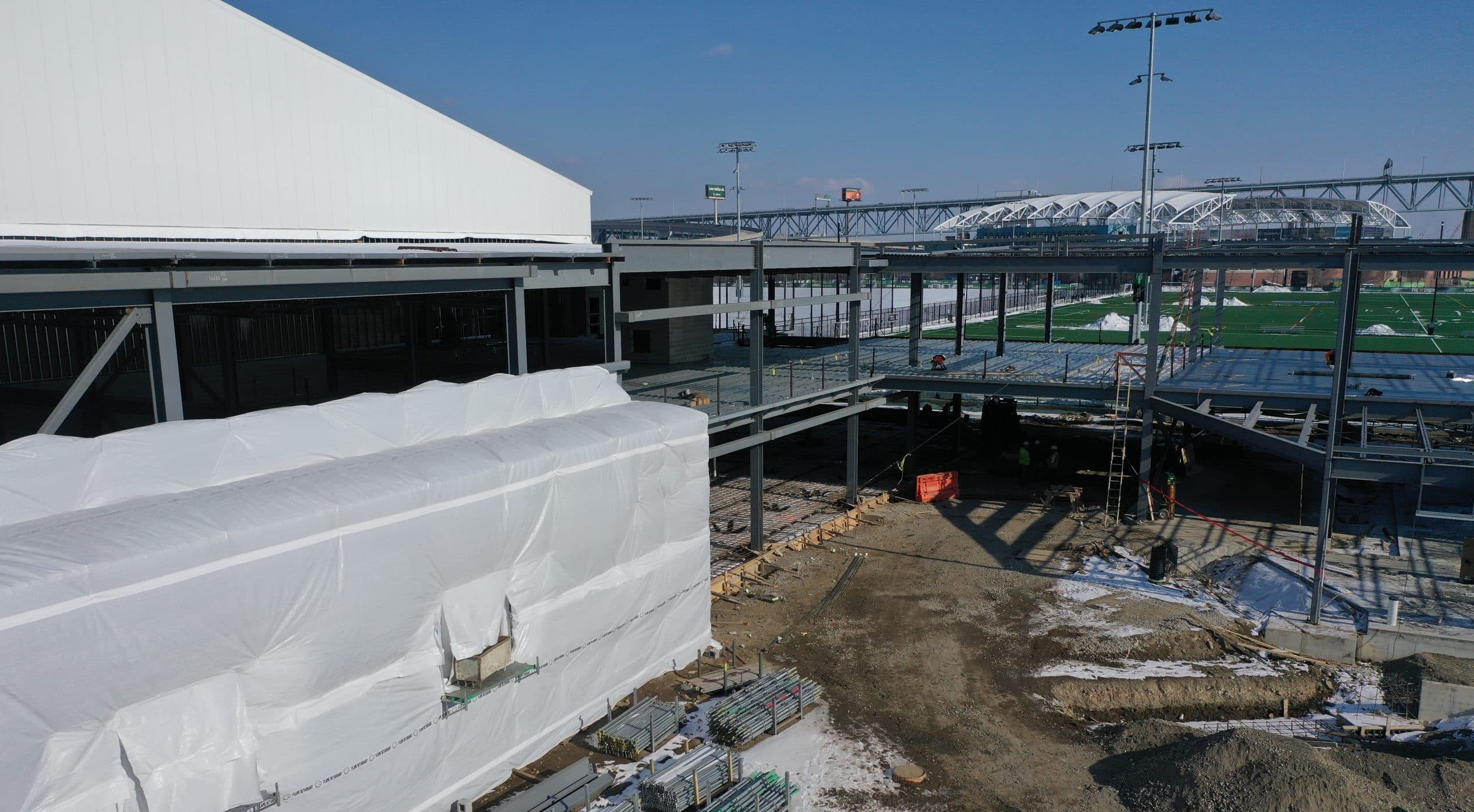
Build and Learn: Cold Weather Construction
February 12, 2025 9:40 pmAt BPGS Construction, continuous learning is a crucial part of the company culture. BPGS is dedicated to empowering associates with knowledge to further their careers while also fostering an environment of comradery. Through the years, the team has developed strategic Build and Learn sessions in which all associates gather at a current job site for a lesson on unique aspects of the project or discussion on how an obstacle was overcome.
Cold weather construction is a common challenge in the industry, particularly in regions like the Mid-Atlantic. Low temperatures can lead to delayed timelines, material failures, budget increases, and worker safety concerns—challenges that can significantly impact any project. At BPGS Construction, we’ve developed a proactive strategy to navigate these obstacles, keeping projects on track and ensuring our teams remain safe. The team at the WSFS Bank Sportsplex recently hosted this month’s Build and Learn to explain how BPGS manages the impact of cold weather. Here’s how we approach these challenges and why our methods set us apart.
Protect Materials from the Cold
Cold temperatures can cause serious issues with materials like concrete and masonry. Water in mixtures can freeze, causing cracks or failures. To avoid this, use additives like calcium chloride or superplasticizers in the mix. Additionally, use insulated blankets to protect materials from freezing. Always monitor the temperature of concrete and rebar to ensure they stay above freezing.
Keep Workers Safe and Comfortable
Worker safety is crucial when temperatures drop. Ensure your crew wears proper clothing, like layers and gloves, to stay warm. Create warm break areas for them to rest. Clear snow and ice from the work area to prevent slips. Safety measures reduce accidents and ensure work continues smoothly.
Use Temporary Heat to Protect Your Worksite
Temporary heating helps maintain the right conditions inside buildings. Depending on your needs, use propane, natural gas, or electric heaters. Make sure to close off openings to prevent heat loss. Keep an eye on the temperature to ensure a safe, workable environment. Heating costs may rise, but they’re necessary to prevent damage and delays.
Plan for Schedule and Budget Delays
Cold weather can slow down progress. Schedule extra buffer time for potential weather-related delays. Be transparent with clients about possible changes to the timeline or budget. Cold weather construction costs can add up, but it’s better to plan for these contingencies than to be caught off guard.
Above all, managing cold weather construction projects require preparation. Protect materials, ensure worker safety, use temporary heat, and plan for delays. By having a proactive strategy in place, projects can continue to progress smoothly, no matter the temperature.
If you’re passionate about continuous learning, teamwork, and tackling challenges head-on (like mastering cold weather construction), we’d love to have you on our team. Explore our current job opportunities and see how you can grow with us.