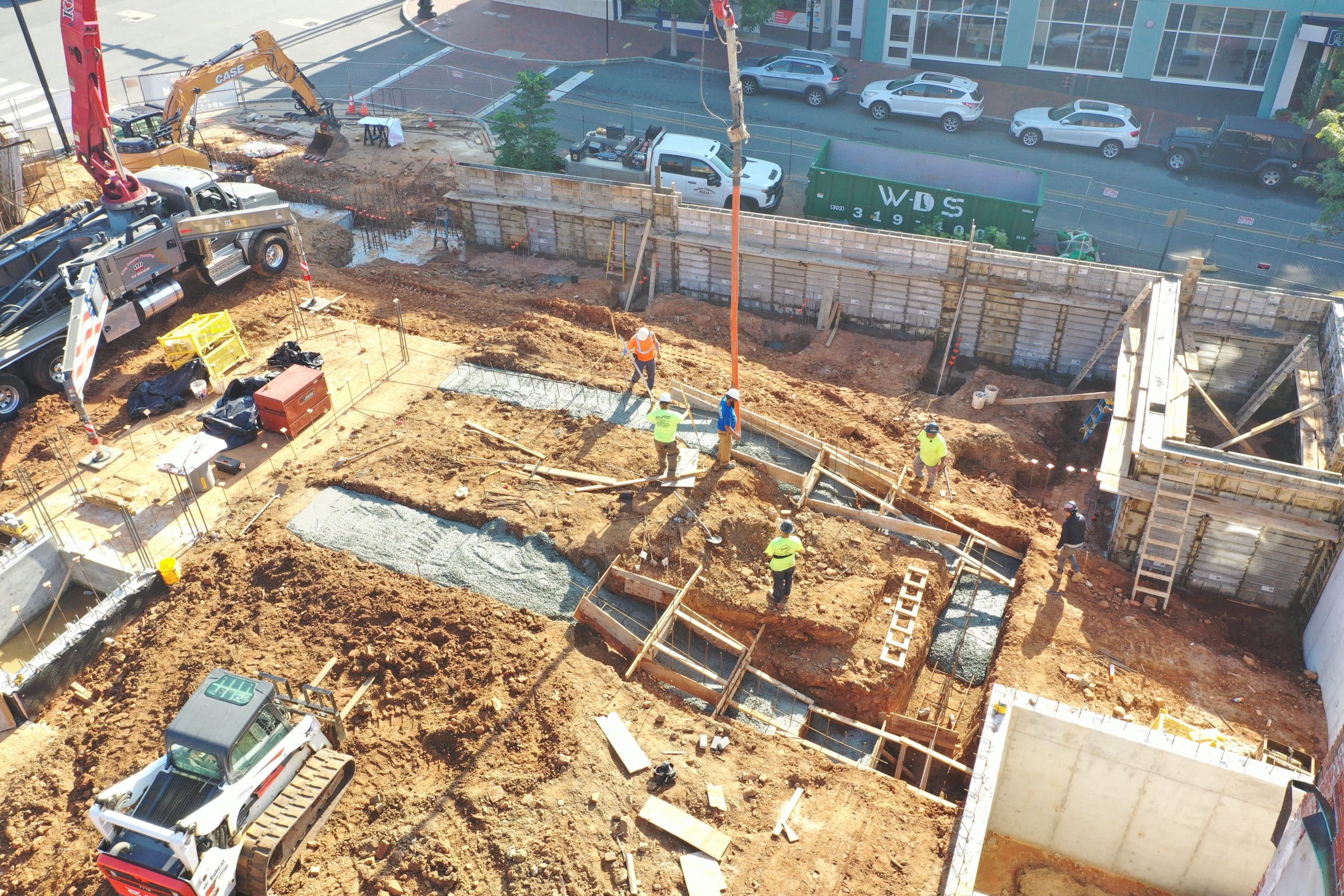
Build & Learn: Geotech Reporting and Concrete Footings at Humble Park
October 11, 2023 6:32 pmAt BPGS Construction, continuous learning is a crucial part of the company culture. BPGS is dedicated to empowering associates with knowledge to further their careers while also fostering an environment of comradery. Through the years, the team has developed strategic Build and Learn sessions in which all associates gather at a current job site for a lesson on unique aspects of the project or discussion on how an obstacle was overcome.
This month, Project Engineer David Summerfield discussed geotechnical reporting and concrete footings in relation to Humble Park in Wilmington, DE. The project is a 63,000 SF apartment community featuring 6-stories and 61-units. The building will consist of a Slab-on-Grade (SOG) with cold-formed metal framing on level one, a ComSlab Elevated Deck on level two, and wood framing on levels two through six. The façade is made of brick, fiber cement, Exterior Insulation Finishing System (EIFS), and aluminum windows.
Geotechnical Report
Prior to the start of development, the site underwent a geotechnical investigation to assist in the design and construction planning for the newly proposed multi-family development. The investigation consisted of drilling (5) test borings, a visual evaluation and classification of the collected soil samples, (6) test pits to determine the accuracy of the borings, and an engineering analysis of the data. A Geotechnical Report of Humble Park was generated to summarize the sites subsurface conditions.
The report concluded that the site contained Soil Type C, the least stable type of soil which is made up of mixed, loose, and granular gravel, sand, and submerged soil. Due to the potential for loose zones and variable strength and consistency throughout the fill mass (material encountered beneath the ground surface), the existing material was not considered capable of supporting foundations for the proposed structure. Based on the recommendations in the report, the BPGS team agreed to undercut to the underlying alluvial soils 10’ from grade. The material was stockpiled, sifted through, put back and compacted in 1’ lifts to meet the required bearing levels for foundations. Since the excavation of the fill was greater than five feet, the project team utilized sloping as the method of protecting workers from cave-ins. Sloping is the process of excavating to form sides of an excavation that are inclined away so as to prevent cave-ins, for type c soil the slope angle must not be greater than 34 degrees.
Concrete Footings
Due to the variance in elevation throughout the construction site, the project team is utilizing stepped concrete footings to ensure a solid foundation. Stepped footings are a form of concrete foundations that follow the the elevations of the grade, and help to transition from deep foundation to shallow ones. Advantages of stepped footings include:
- Erosion control: the footings match the contours of the slope and therefore will have less impact on the surrounding soil and prevent erosion
- Cost-effective: stepped footings minimize the cost of excavation as you only need to excavate what is needed for each step
- Flexibility: the footings can be adapted to fit the site conditions
The project is expected to be completed in Summer of 2024.
BPGS encourages our teams to employ creative solutions in order to get the job done. If this sounds like you, click here for current opportunities!